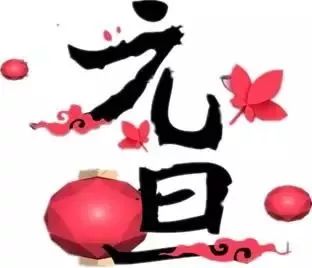
Powders and Granules
Main Unit |
Sub Unit |
Details |
Key Points |
II. Powders and Granules |
(1) Introduction to Powder Science |
Properties and Applications of Powders |
(1) Particle size, size distribution, and measurement methods of powders(2) Specific surface area, porosity, density, flowability, hygroscopicity, and wettability of powders(3) Applications of powder science in pharmaceutics |
(2) Powders |
1. Characteristics and Classification of Powders |
(1) Characteristics(2) Classification |
|
2. Preparation of Powders |
(1) Pre-treatment of materials(2) Purpose, significance, and methods of grinding(3) Purpose, significance, influencing factors, and classification of sieving(4) Purpose and methods of mixing |
||
3. Quality Inspection of Powders and Examples of Hygroscopicity |
(1) Quality inspection items and limits(2) Hygroscopicity of powders and preventive measures(3) Formulation analysis, preparation process, and operational key points of powders |
||
(3) Granules |
1. Characteristics and Classification of Granules |
(1) Characteristics(2) Classification |
|
2. Preparation of Granules |
Preparation process |
||
3. Quality Inspection of Granules |
Quality inspection items and limits |
Introduction to Powder Science
(1) Concept of Powder SciencePowder Science (mlcromeritics) is an applied science that studies the surface properties, mechanical properties, electrical properties, and other aspects of solid particle aggregates (referred to as powders).Due to the need for grinding, mixing, and other treatments of raw and auxiliary materials in the production of solid preparations such as powders, granules, tablets, and capsules, the various properties of powders play a significant role in solid formulations.(2) Properties of Powders1. Particle size, size distribution, and measurement methods of powders(1) Particle size and size distribution of powdersThe particle size of powders is the most fundamental property, significantly affecting the solubility, compressibility, density, flowability, etc., of powders, thereby influencing drug dissolution and absorption. Common methods for expressing particle size include:①Directional Diameter: The diameter measured in the same direction under a microscope.②Equivalent Diameter: The diameter of the circumscribed circle of the particle.③Volume Equivalent Diameter: The diameter of a sphere with the same volume as the particle, measurable using a Coulter counter.④Effective Diameter: The diameter calculated based on the sedimentation formula (Stokes’ equation), also known as Stokes diameter.⑤Sieving Diameter: The diameter measured using the sieving method, generally expressed as the arithmetic or geometric mean of the sieve hole diameters.The size of powders cannot be uniform; there exists a problem of size distribution, and uneven distribution can lead to issues such as inaccurate dosing, variations in compressibility, and changes in particle density. Therefore,studying particle size distributionis also of significant importance.Common frequency distributions represent the percentage of particles of each size relative to the total particle population.
(2) Measurement methods for particle size of powders①Microscopic Method: The microscopic method involves placing particles under a microscope and measuring the particle size based on the projected image. Optical microscopes can measure particle sizes in the range of0.5–100μm. During measurement, care should be taken to avoid overlapping particles to prevent measurement errors, and the number of measured particles shouldhave statistical significance, generally requiring the measurement of200–500particles.②Coulter Counting Method: The Coulter counting method involves filling a measuring tube with an electrolyte solution, suspending the particle population in the electrolyte solution, and measuring the change in current as particles pass through a small aperture between electrodes, which can then be converted into particle size. This method can be used to determine the particle size distribution ofsuspensions, emulsions, liposomes, and powdered drugs.③Sedimentation Method: The sedimentation method calculates particle size based on Stokes’ equation and is suitable for measuring particle sizes below100μm.④Sieving Method: The sieving method is the earliest and most widely used method for measuring particle size. It involves arranging sieves in order of aperture size, placing a certain amount of powder sample on the top sieve, and vibrating for a specified time at a certain frequency, weighing the powder on each sieve to determine the percentage of different particle sizes. The common measurement range is above45μm.When measuring particle size, it is important to note that a reasonable selection and treatment of samples before analysis is the basis for obtaining correct conclusions. When selecting samples, it is necessary to adopt certain sampling methods due to the potential uneven distribution of particles caused by changes in storage conditions or transfer. To ensure representative sampling, an appropriate sampling amount should be used.
2. Specific Surface Area of PowdersSpecific surface area is a measure of the fineness of particles in powders and their solid adsorption capacity. The surface area of particles includes not only the external surface area but also the internal surface area formed bycracksandpores.Common methods for directly measuring the specific surface area of powders includegas adsorption methods.3. Porosity of PowdersPorosity is the ratio of the total voids in powders. Total voids includepores within the powderandvoids between powders. Thefilled volume (V) of powders is the sum of thetrue volume (Vt),pore volume within the powder (Vin),and void volume between powders (Vbetween).Methods for measuring porosity include mercury intrusion and gas adsorption methods. The common method for measuring the porosity of powders involves measuring the volume of liquid displaced by immersing the powder in a liquid after degassing by heating or reducing pressure, thus determining the porosity.4. Density of Powders The density of powders has different meanings and can be expressed in three ways:①True Density: The density calculated by dividing the mass of the powder (M) by the volume excluding the internal and external voids (M/Vt).②Particle Density: The density calculated by dividing the mass of the powder (M) by the volume including the internal voids (M/(Vt+Vin)).③Bulk Density: The density calculated by dividing the mass of the powder (M) by the volume occupied by the powder in the container (M/V, V=Vt+Vin+Vbetween), also known as tapped density.The methods for measuring true density and particle density are consistent with the corresponding methods for measuring porosity. When measuring bulk density, the density measured without applying any external force during filling is referred to as the loosest (bulk) density, while the density measured under the tightest filling state with applied force is referred to as the tightest (bulk) density.
5. Flowability of Powders(1) SignificanceThe flowability of powders is related to various factors, and thus cannot be represented by a single index. However, the flowability of powders significantly affects theweight differences in formulations such as granules, capsules, and tablets, making it an important aspect affecting product quality. There are various forms of powder flow, and corresponding evaluation methods for flowability also vary; this article will only introduce commonly used methods.The angle of repose is the maximum angle formed between the free surface of a powder pile and the horizontal plane.Common measurement methods include the injection method, discharge method, and angle of inclination method, as shown in Figure 2-2. The angle of repose can be measured directly or calculated based on the height and radius of the powder layer, i.e., tanθ=height/radius.
(2) Evaluation Methods:Angle of Repose: The smaller the angle of repose, the lower the friction, and the better the flowability, generally considered acceptable for production flowability when θ≤40°.Flow Rate: The flow rate is the time required for all the powder to flow out when added to a funnel.Inter-particle adhesion, friction, van der Waals forces, and electrostatic forces often hinder the free flow of particles, affecting the flowability of powders.
(3) Measures to Improve Powder Flowability:1) Granulation can reduce the number of contact points between particles, lowering inter-particle adhesion and cohesion;2) Adding a certain amount of coarse powder can improve flowability to some extent;3) The smooth surface of spherical particles reduces the number of contact points, thereby reducing friction and improving flowability. Therefore, various methods can be used toimprove particle shape, making it as close to a regular shape with fewer edges as possible;4) Since powders have hygroscopic properties, moisture adsorbed on the particle surface often increases inter-particle adhesion, thusappropriate drying is beneficial to weaken inter-particle forces. However, excessive drying may decrease flowability due to static electricity;5) Adding 1%–2% of approximately 40μm talc powder, micro-silica gel, etc., asflow aids can smooth the rough surfaces of powder particles, reducing motion resistance and significantly improving flowability. However, excessive flow aids may increase resistance.6. Hygroscopicity of PowdersWhen drug powders are placed in humid air, they are prone to varying degrees of hygroscopicity, leading to decreased flowability, caking, and even affecting drug stability. The hygroscopicity of water-soluble and water-insoluble drugs differs significantly.Water-soluble drug powders generally absorb less moisture in relatively low humidity environments, but when the relative humidity increases to a certain value, the moisture absorption increases sharply; this relative humidity is referred to ascritical relative humidity (CRH). This value can be determined using graphical methods, and CRH is an inherent characteristic of water-soluble drugs, serving as an indicator of hygroscopicity. The smaller the CRH value, the easier it is to absorb moisture; conversely, the larger the CRH value, the less hygroscopic it is. The determination of CRH is usually done using saturated solution methods.Characteristics:1) When severalwater-soluble drugs are mixed, their hygroscopicity has the following characteristics: “The CRH of the mixture is approximately equal to the product of the CRH of each drug,CRHAB=CRHA×CRHB, and is independent of the ratio of each component.” This is known as the Elder hypothesis, but it does not apply to drugs with interactions or common ion effects. For example, the CRH values of glucose and sodium ascorbate are 82% and 71%, respectively; according to the Elder hypothesis, the CRH value of their mixture would be 58.3%, while the experimentally measured value is 57%, which is consistent.2) The hygroscopicity of water-insoluble drugs changes slowly with variations in relative humidity, without a critical point. The hygroscopicity of mixtures of water-insoluble drugs exhibits additivity.7. Wettability of PowdersThe wettability of powders is significant for the disintegration and solubility of solid preparations such as tablets and granules. The wettability of powders is represented by the contact angle. The minimum contact angle is0°, and the maximum is 180°.The smaller the contact angle, the better the wettability of the powder.(3) Applications of Powder Science in PharmaceuticsAs raw materials, particle size is often overlooked, but when formulating, it must meet certain requirements. The particle size of drugs can affect the appearance quality, color, taste, uniformity of content, stability, and bioavailability of formulations.
Powders
(1) Concept, Characteristics, and Classification of Powders1. Definition:Powders (粉剂) refer to drug or suitable auxiliary materials that are crushed and uniformly mixed to form a dry powder preparation. They are divided into oral powders and topical powders.Oral powders are generally dissolved in or dispersed in water or other liquids for administration, and can also be taken directly with water. Topical powders can be applied to the skin, oral cavity, throat, and cavities; powders specifically for treating, preventing, and lubricating the skin can also be referred to as dusting powders.2. Classification:① According to the number of medicinal ingredients, they can be divided into single powders and compound powders;② According to dosage, they can be divided into divided-dose powders and undivided-dose powders;③ According to purpose, they can be divided into solution powders, decoction powders, blowing powders, internal-use powders, external-use powders, etc. For example, Xiaoer Qingfei San is for oral use, while prickly heat powder is an external-use powder.3. Characteristics:① High degree of grinding, large specific surface area, easy dispersion, and rapid action;② Large coverage area for external use, providing protective and astringent effects;③ Simple preparation process, easy dosage control, and convenient for children to take;④ Convenient for storage, transportation, and carrying.
(2) Preparation of PowdersProcess Flow:
1. Pre-treatment of MaterialsIn solid dosage forms, the term “materials” usually refers to both drugs and auxiliary materials. Therefore, the so-called pre-treatment of materials refers to processing the materials to meet the requirements for grinding. If it is Western medicine, the raw and auxiliary materials should be sufficiently dried to meet the grinding requirements; if it is Chinese medicine, appropriate treatment should be conducted based on the properties of each medicinal material in the prescription to ensure they are dried to clean medicinal materials for grinding.2. Grinding(1) Concept and Significance of Grinding1) Concept of GrindingGrinding is the process of breaking large materials into smaller particles or powders, primarily aimed at reducing particle size and increasing specific surface area. When the particle shape is fixed, the smaller the particles, the larger their specific surface area. When the particle size is reduced to one-tenth, the total surface area can increase significantly. Generally,the ratio of the particle size before grinding (D) to the particle size after grinding (d) is referred to as the degree of grinding.2)Significance of Grinding① Fine powders facilitate the dissolution and absorption of solid drugs, improving the bioavailability of poorly soluble drugs;② Fine powders facilitate the uniform mixing of components in solid preparations, and the degree of uniformity is related to the particle size of each component;③improves the dispersibility of solid drugs in liquids, semi-solids, and gases, enhancing the quality and efficacy of formulations;④helps extract active ingredients from natural drugs, etc. (2) Mechanism, Methods, and Equipment for Grinding① Mechanism of Grinding:Substances aggregate into a certain shape due to their intermolecularcohesive forces. The grinding process primarily relies on the application of external mechanical forces to break the cohesive forces between molecules. Common external forces used in the grinding process include: impact, compression, cutting, bending, and rubbing.② Methods of Grinding:Grinding methods can be classified based on the state, composition, environmental conditions, and dispersion methods of the material being ground, including dry grinding, wet grinding, separate grinding, mixed grinding, cryogenic grinding, and fluid energy grinding. The more commonly used methods aredry grinding and wet grinding; dry grinding involves drying the drug to a certain extent (generally to less than 5% moisture) before grinding, while wet grinding refers to adding an appropriate amount of water or other liquids to the drug powder before grinding, which can reduce the mutual adhesion and aggregation of drug powders, improving grinding efficiency.Depending on the properties of the material being ground, the required particle size, and the grinding equipment, grinding can be classified into:A. Closed grinding and open grinding.B. Open grinding and circulating grinding.C. Dry grinding and wet grinding.D. Cryogenic grinding.E. Mixed grinding.③ Grinding EquipmentA. Ball Mill: Due to its high grinding efficiency, good sealing, and low dust generation, it has a wide range of applications; it can performboth dry and wet grinding; it can grind toxic, precious, hygroscopic, or strongly irritating drugs, and can also grind easily oxidizable drugs under inert gas conditions, and can be used for sterile grinding of ophthalmic and injectable drugs; for crystalline drugs and hard, brittle drugs, the ball mill is particularly effective, generally achieving ultra-fine powders that can pass through a 200-mesh sieve.B. Impact Mill: The impact mill primarily uses impact force on materials, suitable for brittle and tough materials, as well as for medium, fine, and ultra-fine grinding, widely used, hence known as the “universal grinder.” Its typical grinding structures include hammer and impact column types.C. Airflow Mill: Also known as fluid energy mill, its grinding power comes from high-speed airflow, commonly used for ultra-fine grinding of materials, thus known as the “micro powder machine.” Due to the high-pressure airflow (170–2070kPa) expanding and absorbing heat during the grinding process, it produces a significant cooling effect, which can offset the heat generated during grinding, making it suitable for grinding heat-sensitive materials and low-melting-point materials.In summary, the characteristics of airflow grinding include:① It can achieve ultra-fine grinding with a particle size requirement of 3–20μm;② Due to the cooling effect generated by high-pressure air exiting the nozzle, it is suitable for grinding heat-sensitive and low-melting-point materials;③ The equipment is simple, and it is easy to perform sterile treatment on the machine and compressed air, making it suitable for grinding sterile powders;④ Compared to other grinders, the grinding cost is high, but it is worthwhile when high particle size requirements are needed.D. Colloid Mill: The colloid mill is a wet grinding machine. A typical colloid mill consists of a stator and rotor, where the rotor rotates at high speed, and the material is ground into a colloidal state under the shear force between the stator and rotor. The ground product is expelled from the gap due to the centrifugal action of the rotating rotor. The colloid mill is commonly used for grinding dispersions such as suspensions and emulsions.E. Roller Mill: The roller mill is commonly used for grinding semi-solid dispersions, such as the grinding of materials in ointments, suppositories, etc. The material passes through the gap between two counter-rotating rollers, where it is ground under the action of compressive and shear forces.3. Sieving(1) Sieving: This is the method of separating particle populations based on size, specific gravity, charge, and magnetic properties.Sieving is a method of separation using the size of sieve holes, which is simple, economical, and has high grading accuracy, making it the most widely used particle classification operation in the pharmaceutical industry.(2) Purpose of Sieving: In summary, it is toobtain a more uniform particle population, either by sieving out coarse powder to obtain fine powder, or sieving out fine powder to obtain coarse powder, or sieving out both coarse and fine powders to obtain medium powder, etc. This is of great significance for the quality of drugs and the smooth progress of formulations.(3) Sieves used for sieving: There are two types based on their manufacturing methods, one is the punched sieve, also known as the molded sieve, which is made by punching circular holes in a metal plate. Its holes are sturdy and not easily deformed, commonly used for the sieve plates of high-speed rotating grinders and for sieving coarse particles in pills. The other is the woven sieve, made of metal wires (such as stainless steel, copper wire, iron wire, etc.) or other non-metallic wires (such as silk, nylon, silk, etc.). The advantage of woven sieves is that they have more holes per unit area, high sieving efficiency, and can be used for fine powder sieving. Non-metallic sieves have certain elasticity and durability. Nylon wire is relatively stable for general drugs and is widely used in formulation production, but woven sieve wires can easily shift, causing deformation of sieve holes and decreased separation efficiency.(4) The standard sieves used in industrial applications in China are commonly indicated by the “mesh” number, which represents the number of sieve holes per inch (25.4mm) in length, but there is no unified standard specification. The mesh number does not accurately reflect the size of the holes, as the diameter of the sieve wire used varies, leading to different hole sizes; thus, the specific size of the holes must be indicated, commonly expressed in μm. For example, a sieve with 100 holes per inch is marked as a 100-mesh sieve, and powders that can pass through a 100-mesh sieve are referred to as 100-mesh powder.(5) The sieves used in the Chinese Pharmacopoeia select the national standard R40/3 series, and the relationship between the sieve number and the average inner diameter of the sieve holes is as follows:Sieve NumberAverage Inner DiameterMesh Number1st Sieve2000μm±70μm10 Mesh2nd Sieve850μm±29μm24 Mesh3rd Sieve355μm±13μm50 Mesh4th Sieve250μm±9.9μm65 Mesh5th Sieve180μm±7.6μm80 Mesh6th Sieve150μm±6.6μm100 Mesh7th Sieve125μm±5.8μm120 Mesh8th Sieve90μm±4.6μm150 Mesh9th Sieve75μm±4.1μm200 Mesh(6) Classification of Solid PowdersTo facilitate the distinction of solid powders, they are classified into the following six grades:The coarsest powder: refers to powder that can pass through the first sieve but contains no more than 20% of powder that can pass through the third sieve;The coarse powder: refers to powder that can pass through the second sieve but contains no more than 40% of powder that can pass through the fourth sieve;The medium powder: refers to powder that can pass through the fourth sieve but contains no more than 60% of powder that can pass through the fifth sieve;The fine powder: refers to powder that can pass through the fifth sieve and contains no less than 95% of powder that can pass through the sixth sieve;The finest powder: refers to powder that can pass through the sixth sieve and contains no less than 95% of powder that can pass through the seventh sieve;The ultra-fine powder: refers to powder that can pass through the eighth sieve and contains no less than 95% of powder that can pass through the ninth sieve.
(7) Factors Affecting SievingTo improve sieving efficiency, the influencing factors of the sieving operation are summarized as follows:① Particle Size Range:The smaller the particle size of the drug, the more likely it is to aggregate into clumps or block sieve holes due to surface energy, static electricity, etc., making it difficult to operate; generally, the sieving particle size should not be less than 70–80μm. When the particle size is close to the boundary diameter (i.e., sieve hole diameter), separation becomes more difficult;② Moisture Content:Increased moisture content in the material increases viscosity, making it prone to clumping or blocking sieve holes;③ Particle Shape and Properties:Irregular particle shapes and surface conditions, low density, etc., make it difficult for the material to pass through the sieve;④ Parameters of the Sieving Device:Such as the inclination angle of the sieve surface, vibration mode, movement speed, sieve area, thickness of the material layer, and sieving time, ensuring sufficient contact between the material and the sieve surface, providing opportunities for small particles to pass through the sieve holes.4. Mixing and Dividing DosesThe operation of uniformly mixing two or more components is referred to as mixing, which includes solid-solid, solid-liquid, and liquid-liquid mixing. The purpose of mixing is to achieve uniformity in content.However, different systems and purposes require different operational methods. This section mainly introduces the mixing of solids, i.e., solid-solid particle mixing.Pharmaceutical solid micro-powders have the following characteristics:① A wide variety of powders;② Irregular shapes, sizes, and surface roughness of particles;③ Small particle size and density, strong adhesion, cohesiveness, and dispersibility;④ Multiple components, sometimes reaching dozens;⑤ In micro-mixing, the minimum mixing ratio (dilution ratio) is relatively large, which brings certain difficulties to the mixing operation.(1) Brief Introduction to Mixing MechanismsThe mixing mechanism can be summarized into three types of motion:①Convective Mixing: This is the overall mixing that occurs when solid particle populations are displaced significantly under mechanical rotation.②Shear Mixing: This is the result of internal forces within the particle population, creating sliding surfaces that disrupt the cohesive state of the particle population for local mixing.③Diffusion Mixing: This occurs when adjacent particles exchange positions due to random motion, happening when particles roll down an inclined sliding surface.(2) Mixing Methods and EquipmentThe grinding mixing method is suitable for small quantities of drug mixing, commonly using a mortar. Common laboratory mixing methods include stirring mixing, grinding mixing, and sieving mixing.For highly toxic drugs, precious drugs, or cases where the mixing ratio of components varies significantly, the “incremental equal quantity” principle should be used for mixing.In large-scale production, the mixing process often employs methods that cause the container to rotate or stir, allowing for both overall and local movement of materials to achieve mixing. Solid mixing equipment can be broadly divided into two categories: container-rotating and container-fixed.① Container-Rotating Mixers: These are devices that rely on the rotation of the container to drive the material up and down for mixing.A. Horizontal Cylinder Mixers: These mixers have lower mixing efficiency but are simple in structure and low in cost.B. V-Type Mixers: These mixers have top feeding and bottom discharging, can operate in a closed environment, improve conditions, reduce labor intensity, and are suitable for mixing wet and viscous powder materials.C. Double Cone Mixers: The mixing effect is similar to that of V-type mixers.② Container-Fixed Mixers: These are devices that mix materials in a container through the stirring action of blades, screws, or airflow.(3) Factors Affecting Mixing Effectiveness and Measures to Prevent Uneven Mixing① Component Ratio:Two powders with similar properties and densities can be mixed uniformly after a certain time, but when there is a significant difference in quantity or component ratio, it becomes difficult to achieve uniform mixing. In such cases, the “incremental equal quantity mixing method” (also known as the “proportional mixing method”) should be used, where small quantities of drugs are finely ground and mixed with equal volumes of other fine powders, gradually increasing the mixing until all components are uniformly mixed, followed by sieving mixing.② Density of Components:Two powders with similar properties and densities mix easily, but if there is a significant density difference, the lighter (lower density) powder should be placed in the mixing container first, followed by the heavier (higher density) powder, to avoid the lighter powder floating on top or flying away while the heavier powder settles at the bottom and becomes difficult to mix.③ Adsorption and Charge Properties of Components:Some drug powders have adhesive properties to mixing equipment, affecting mixing and causing losses. Generally, the larger and less adhesive powders or auxiliary materials should be placed at the bottom, while smaller and more adhesive powders should be added later. Powders that become charged due to mixing friction often hinder uniform mixing; a small amount of surfactant can be added to overcome this, and some people use lubricants as anti-static agents, such as adding 0.25%–0.5% magnesium stearate to aspirin powder for anti-static effects.④ Components Containing Liquids or Hygroscopic Properties:If the powder contains such components, appropriate measures should be taken before mixing to ensure uniform mixing. For example, if the prescription contains liquid components, other components in the prescription can be used to absorb the liquid; if the liquid component is too much, it is advisable to use absorbents until no wetting is observed. Common absorbents include calcium phosphate, white clay, sucrose, and glucose. If there are hygroscopic components, measures should be taken to address the hygroscopicity:A. If it contains crystallized water (which may cause wetting due to grinding), it can be replaced with an equivalent amount of anhydrous substance;B. If it is a highly hygroscopic drug (such as pepsin), it should be mixed rapidly under conditions below its critical relative humidity and sealed in moisture-proof packaging;C. If components become hygroscopic due to mixing, they should not be mixed and can be packaged separately.⑤ Components that Can Form Low Eutectic Mixtures:When two or more drugs are mixed in a certain ratio, the phenomenon of wetting and liquefaction that occurs at room temperature is referred to as the low eutectic phenomenon. This phenomenon is detrimental to the mixing of components.(4) Dividing DosesDividing the uniformly mixed powders into equal weight portions according to weight requirements is called dividing doses. Common methods include visual inspection, weight method, and volume method. Mechanical production often uses the volume method for dividing doses. To ensure the accuracy of the dosage, necessary experimental investigations should be conducted on the physical and chemical properties of the drug powder, such as flowability, hygroscopicity, and density differences.
5. Quality InspectionThe quality of powders is closely related to the preparation process and hygroscopicity.(3) Quality Inspection of Powders and Examples of Hygroscopicity.[Key Points] Quality Inspection: Items and Limits1. Quality Inspection The Pharmacopoeia includes quality inspection items for powders, mainly including:(1) Particle Size: Unless otherwise specified, for topical powders, the following method is used for inspection, and the particle size should meet the requirements.Inspection Method: Take 10g of the sample, weigh it precisely, place it on a7th sieve, cover the sieve, and place a tightly sealed receiving container below. Inspect according to the “Particle Size and Size Distribution Determination Method” (Chinese Pharmacopoeia 2005 Edition, Volume II, Appendix 1XE, Single Sieve Method), and the weight of the powder passing through the sieve shouldnot be less than 95%.(2) Uniformity of Appearance: Take an appropriate amount of the sample, spread it on smooth paper to about 5cm2, flatten the surface, and observe in bright light; it should present a uniform color without patterns or spots.(3) Loss on Drying: Unless otherwise specified, take the sample and measure according to the “Loss on Drying Determination Method” (Chinese Pharmacopoeia 2005 Edition, Volume II, Appendix VIII1), drying at 105°C until constant weight, and the weight lossmust not exceed 2.0%.(4) Dose Variation: The dose variation limits for single-dose packaged powders should meet the following relevant regulations.Inspection Method: Take 10 packages (bottles) of the powder, remove the packaging; weigh the contents of each package (bottle) precisely, calculate the content weight and average weight. The content weight of each package compared to the average weight (for powders without content determination, the content weight should be compared to the labeled weight) should meet the regulations, and no more than 2 packages (bottles) may exceed the dose variation limit, with no package (bottle) exceeding the dose variation limit by more than one time.Table 2-1 Dose Variation Limits for Powders
Average or Labeled Dose |
Dose Variation Limit |
0.1g and below |
±15% |
Above 0.1g to 0.5g |
±10% |
Above 0.5g to 1.5g |
±8% |
Above 1.5g to 6.0g |
±7% |
Above 6.0g |
±5% |
For powders that are required to check content uniformity, the dose variation check may be omitted. In addition, hygiene checks should be conducted according to the “Microbial Limit Inspection Method” in the Chinese Pharmacopoeia, and should comply with relevant regulations.2. Hygroscopicity of Powders and Preventive MeasuresThe focus of powders is on moisture prevention, as powders have a larger specific surface area, their hygroscopicity and weathering properties are more pronounced. If moisture is absorbed due to improper packaging and storage, a series of instability phenomena such as deliquescence, caking, discoloration, decomposition, and mold growth can easily occur, severely affecting the quality of powders and the safety of medication. Therefore, the hygroscopic characteristics of powders and measures to prevent moisture absorption become important aspects of controlling powder quality.When the vapor pressure of water in the air exceeds the saturated vapor pressure generated by the drug powder itself, solid drug powders will adsorb water molecules, a phenomenon generally referred to as hygroscopicity. The hygroscopic characteristics of drugs can be represented by a hygroscopic balance curve, which is obtained by determining the (equilibrium) moisture absorption of the drug at different humidity levels and plotting the moisture absorption against relative humidity, resulting in the hygroscopic balance curve, as shown in Figures 2-8 and 2-9, which represent the hygroscopic balance curves of water-soluble and non-water-soluble drugs (or auxiliary materials), respectively. As seen in Figure 2-8, water-soluble drugs absorb almost no moisture in relatively low humidity environments, but when the relative humidity increases to a certain value, the moisture absorption increases sharply; the relative humidity at which this sharp increase occurs is referred to ascritical relative humidity (CRH).
Determining CRH has the following significance:① The CRH value can serve as an indicator of drug hygroscopicity; generally,the larger the CRH, the less hygroscopic it is;② To control the environmental conditions of production and storage, the relative humidity of the production and storage environment should bekept below the CRH value of the drug to prevent moisture absorption;③ To provide reference for selecting moisture-resistant auxiliary materials, generally, materials withhigh CRH values should be chosen as auxiliary materials.Generally, powders should be stored in sealed containers, and powders containing volatile or hygroscopic components should be especially sealed.Example 1. General Powder (Ice Boron Powder)Prescription:Ice Boron50g, Borax (fried) 500g, Cinnabar 60g, Xuanming Powder 500gPreparation Method: The above four ingredients, Cinnabar is water-fly or ground into ultra-fine powder, Borax is ground into fine powder, Ice Boron is finely ground, mixed with the above powders and Xuanming Powder, sieved, and mixed to obtain.Note: ① Cinnabar mainly contains mercuric sulfide, in granular or block aggregates, bright red or dark red in color, heavy and brittle, and ultra-fine powder can be obtained by water-flying method. Xuanming Powder is obtained from the weathering and drying of Glauber’s salt, containing no less than 99% sodium sulfate. ② The product has colored Cinnabar, making it easy to observe the uniformity of mixing. The content of Ice Boron must not be less than 35%. ③ This product has the functions of clearing heat and detoxifying, reducing swelling and relieving pain, used for sore throat, swollen gums, and mouth ulcers. It can be blown in small amounts several times a day.Example 2. Powder Containing Low Eutectic Components (Prickly Heat Powder)Prescription:Talc Powder 67.7%, Salicylic Acid 14%, Zinc Oxide 6.0%, Boric Acid 8.5%, Sublimed Sulfur 4.0%, Thymol 0.6%, Menthol 0.6%, Camphor 0.6%, Starch 10%Preparation Method: First, grind Thymol, Menthol, and Camphor to form alow eutectic mixture, mix with the above low eutectic mixture containing Menthol, and grind the other ingredients (Sublimed Sulfur, Salicylic Acid, Boric Acid, Zinc Oxide, Starch, Talc Powder) in a ball mill to fine powder, sieving through 100–120 mesh. Place this fine powder in a mixing cylinder (with a spray device), spray in the above low eutectic mixture containing Menthol, mix uniformly, and sieve to obtain.Note: ① The Thymol, Menthol, and Camphor in this product undergo low eutectic mixing during mixing, and this phenomenon is utilized in the preparation process to ensure uniform mixing with other drugs; ② Talc Powder, Zinc Oxide, etc., should be sterilized before use; ③ This product has hygroscopic, anti-itching, and astringent effects, suitable for prickly heat and heat rash.Example 3. Dilution PowderDilution powder is a diluted powder made by adding a certain amount of filler to a small dose of toxic drugs to facilitate the next preparation. The dilution ratio is determined by the dose:Doses of 0.1–0.01g can be prepared into 10-fold powders (i.e., 9 parts diluent mixed with 1 part drug uniformly), 0.01–0.001g can be prepared into 100-fold powders, and doses below 0.001g should be prepared into 1000-fold powders.When preparing 1000-fold powders, the incremental dilution method should be used. Common diluents include lactose, powdered sugar, starch, dextrin, precipitated calcium carbonate, calcium phosphate, white clay, and other inert substances. The proportional mixing method is generally used for preparation, and the balance should be correctly selected for weighing. To facilitate observation of mixing uniformity, a small amount of coloring agent can be added.
Granules
(1) Concept, Classification, and Characteristics of Granules1. Concept: Granules refer to drug and suitable auxiliary materials made into dry granulated preparations with a certain particle size.2. Classification: Granules can be divided into soluble granules (commonly referred to as granules), suspension granules, effervescent granules, enteric-coated granules, sustained-release granules, and controlled-release granules, for oral use.
(2) Preparation of GranulesThe preparation process of granules is similar to that of tablets, but they do not need to be compressed into tablets; instead, the prepared granules are directly packed into bags. The general preparation process of granules is briefly introduced below (see Chapter 3):(3) Quality Inspection of Granules1. Appearance: Granules should be dry, with uniform particle size, consistent color, and no hygroscopicity, caking, or deliquescence.2. Particle Size: Unless otherwise specified, according to the “Particle Size and Size Distribution Determination Method” [Chinese Pharmacopoeia 2005 Edition, Volume II, Appendix IXE, Method 2], the total of those that cannot pass through the first sieve (2000μm) and those that can pass through the fifth sieve (180μm) must not exceed 15% of the tested amount.3. Loss on Drying: Unless otherwise specified, according to the “Loss on Drying Determination Method” (Chinese Pharmacopoeia 2005 Edition, Volume II, Appendix VIII1), dry to constant weight at 105°C, and the weight loss must not exceed 2.0%.4. Solubility: Unless otherwise specified, soluble granules and effervescent granules should be inspected as follows, and solubility should meet the requirements. Soluble granules inspection method: Take 10g of the sample, add 200ml of heated water, stir for 5 minutes, and the soluble granules should completely dissolve or show slight turbidity, but no foreign matter should be present.Effervescent granules inspection method: Take 6 bags of single-dose packaged effervescent granules, place them in beakers containing 200ml of water at a temperature of 15%–25%, and they should rapidly produce gas and form effervescence, with all 6 bags of granules completely dispersing or dissolving in water within 5 minutes.Suspension granules or granules with specified dissolution or release rates may not require solubility testing.5. Dose Variation: The dose variation limits for single-dose packaged granules should meet the following relevant regulations.
Learn more about“Pharmaceutics”related knowledge
Pharmaceutics: Examination Outline
Pharmaceutics: Introduction
Currently, over 100,000 people have followed and joined us